5 Benefits of Wood in Multi-family Projects
July 13, 2023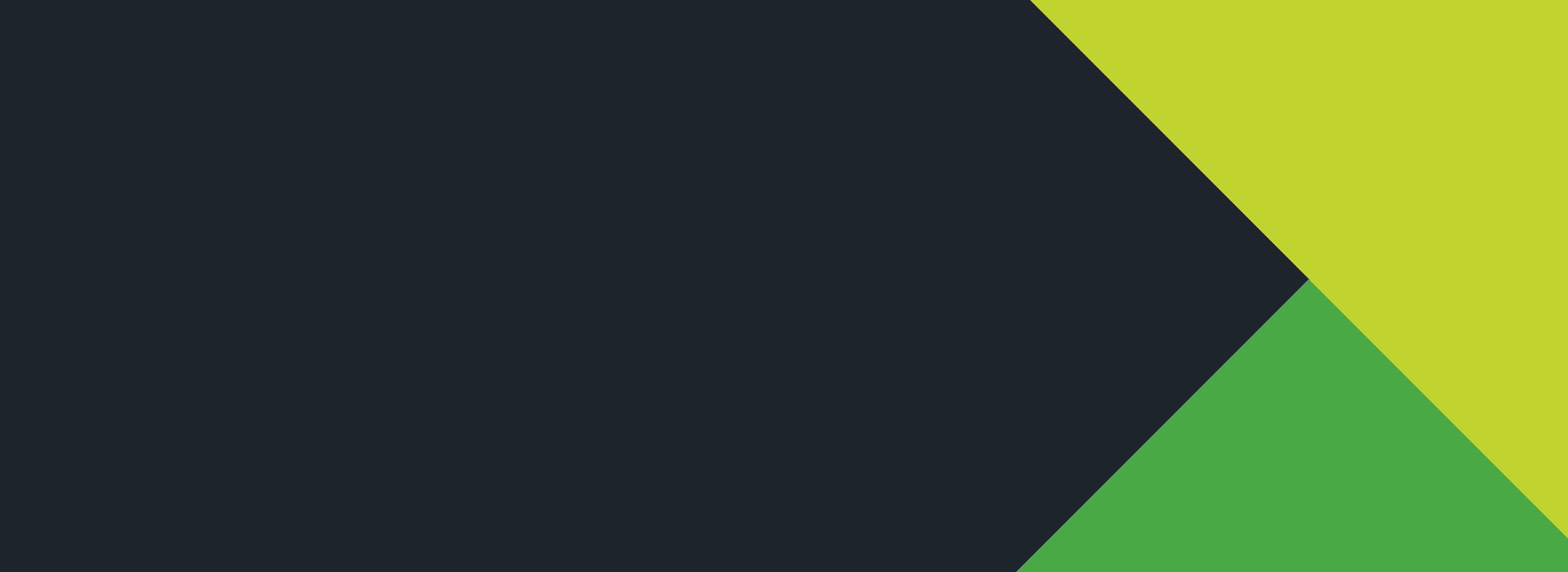
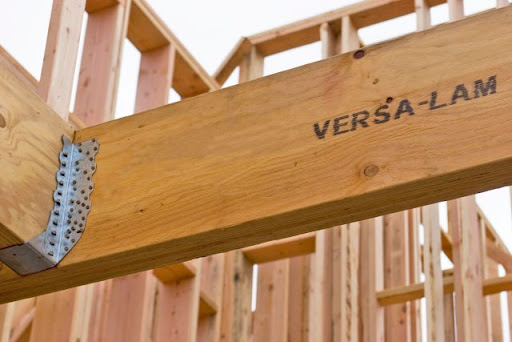
The benefits of wood in multi-family projects
When you think of multi-story multi-family buildings, does your mind automatically envision concrete and steel? It’s time to think again.
Engineered wood products are an ideal option for a multitude of applications across a range of multi-family projects — as well as hotels, senior living, and student housing — offering a number of benefits that address affordability, durability, installation, and more.
Wood is not only suitable for multi-family buildings, but it also offers a number of benefits that make it equal to or better than other materials, in some cases. These include:
- A full range of products, stocked locally: Most of the wood products used in multi-family projects, from glulam to LVL, are manufactured and sold throughout North America, which provides for a reliable supply most of the time. Boise Cascade®, for example, produces material in three different areas of the U.S., helping to get finished product to customers quicker.
- Cost savings: Historically, engineered wood has relatively stable pricing compared to a more volatile commodity product like steel. Localized manufacturing cuts down on transportation costs as well. In addition, wood is familiar to framers, efficient to build with, and customizable through the supply channel, saving time and waste — and the associated costs of each — on site.
- Versatility: Engineered wood products are incredibly versatile — it’s not a matter of “one size,” but rather “what size do you need?” EWP products can be customized to meet the needs of each project. And with our software tools like BC Framer® and BC Connect®, builders can get each piece cut, labeled, and packaged for exact and fast assembly on the jobsite.
- Carbon impact: Embodied carbon is one of the hottest topics in design and construction, as the industry seeks to reduce the significant impact the built environment has on greenhouse gas emissions. Along with engineered wood’s other environmental advantages — it’s made with a readily-renewable material, uses the tree efficiently to reduce waste, and is typically harvested using sustainable forestry practices — it also stores carbon throughout its life and produces far less carbon emissions during manufacturing than concrete and steel.
- Meets fire requirements: Many engineered wood products, including Boise Cascade’s LVL and I-joists, can be used to meet the one and two-hour fire assembly requirements typical of mid-rise multi-family projects, without the need for additional chemicals.
Putting wood to work for affordable housing projects
The Thomas Logan affordable housing project in Boise, Idaho, is just one example of how engineered wood brings multi-family projects to life. Designed and built by Pivot North Architects, Axiom, PLLC, and Andersen Construction, the 65,625-square-foot building features five stories of wood over a two-level concrete podium.
As outlined by Woodworks, the wood used in the project includes:
- 11-7/8”-deep wood I-joists with ¾” OSB subfloor and a 1-inch lightweight concrete topping slab. The floor-ceiling assembly below the I-joists includes resilient channels with two layers of gypsum wallboard for acoustic separation between floors.
The roof was built using wood I-joists topped with wood structural sheathing and tapered insulation for drainage. - Glulam was used to frame shaft openings in each floor, and in stairs to support the landings.
- More than 90% of the wall panels were prefabricated using 2×6 dimension lumber for exterior and corridor walls. Unit demising walls, pre-framed using 2x4s, were doubled with a 1” air gap between to reduce sound transmission.
Read the full case study on the Woodworks website.
Ready to learn more about using wood for multi-family projects?