Atlas Structural Systems: Floor Panel Pioneers
April 9, 2025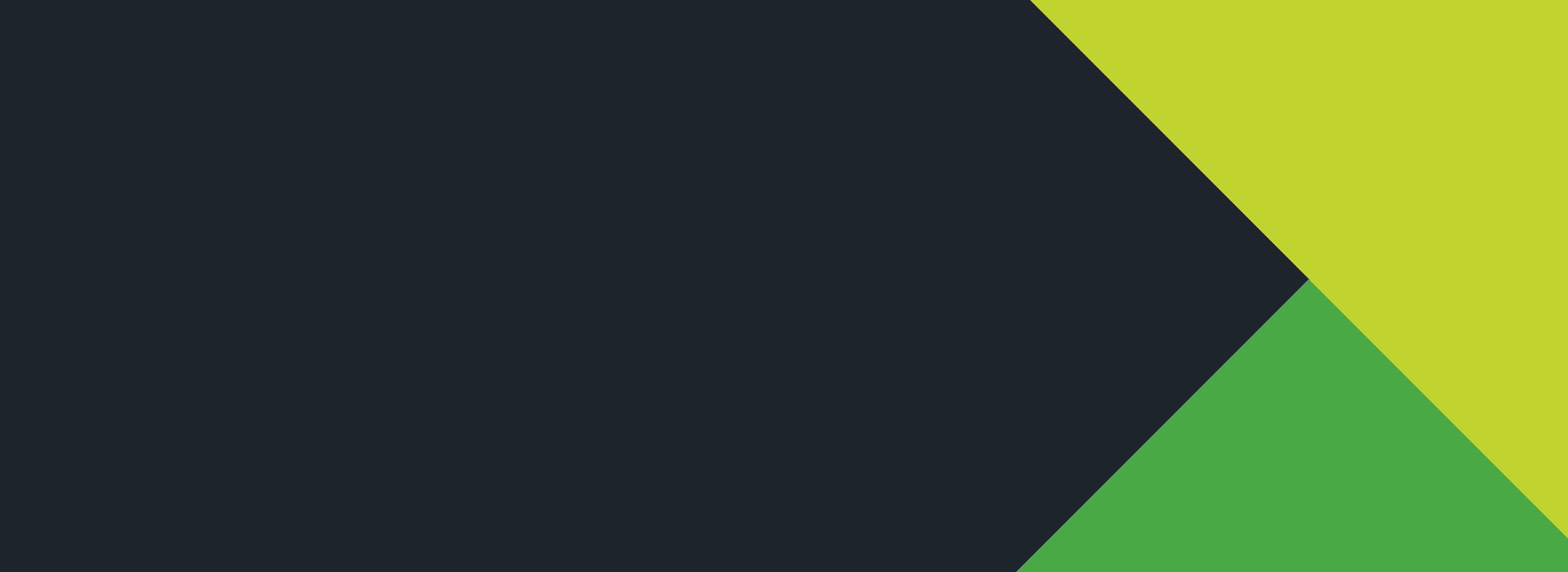
Offering Solutions to Everyday Problems.
The last few years have taught us two important things in the multi-family industry: material and labor are finite. These constraints separated the “can” from the “cannot” and Atlas Structural Systems, an Atlantic Canadian component manufacturer, in this time was able to set themselves apart from the competition. They dialed in their already efficient model and brought success to a market thinned by these finite resources.
The need for high-density housing in Atlantic Canada is tremendously high, similar to other places around the U.S and Canada. A common solution is often 6-story buildings with more than 100 units. These are a great way to quickly house a large number of people, but can it be done faster? Typically, these structure types take 12 months to frame using crews of up to 30 framers when using traditional stick frame methods. This means juggling the workforce between jobsites while complicating an already hectic schedule of trades.
For Atlas Structural Systems, their solution is preassembling both the wall and floor panels in their state-of-the-art manufacturing facility. They’ve found that doing this saves developers and multi-family stick frame builders two things: time and money.
These factory-built panels and floor cassettes are assembled in a controlled environment, where the indoor working conditions lend to a higher degree of precision, consistency, and quality assurance. It also allows for core workers to be retained and help projects run smoothly and more safely from start to finish. That same job that took 12 months and 30 framers now can take six months and a dozen framers to enclose.
“In some parts of the world, stick framing is becoming a thing of the past,” Gerald Hebert of Atlas Structural Systems says. “Our approach became a natural evolution that identified numerous solutions to labor availability, speed of construction, better quality, and a need for more collaborative design.”
Consistency is Key
The key to making their floor panel approach work effectively is a level of consistency versus constructing one-off, stick-built structures fully on-site. For Atlas, they found consistency in products like Boise Cascade AJS® Joists and Versa-Lam LVL®. “The dependability of our engineered wood products helps to streamline their floor panel production process and improves their efficiency and reliability during the construction phase”, says Jeff Bryce, Multi-Family/Light Commercial Manager for Boise Cascade.
Where dimensional lumber can vary in quality and consistency, AJS Joists are manufactured in a production facility with stringent quality controls. They are consistently strong and straight and come with a limited lifetime warranty, which can bring peace of mind to customers like Atlas.
Easier on the Jobsite Starts With Being Smarter in the Factory
As the leading prefabricated panelized floor cassette provider throughout Atlantic Canada, Atlas earned the trust of builders thanks to their willingness to innovate and navigate uncharted waters and deliver solutions in ways that help the bottom line of builders and developers. They went in early, implementing robotics and automation technology to their practices, which allowed them to get a jump on manufacturing panelized floor cassettes and stay ahead by delivering a superior product.
This efficiency and high-quality results are key reasons customers continue to count on Atlas Structural Systems. Their commitment to saving money and time on projects while delivering a product that prioritizes safety and customer satisfaction is integral to their success in a growing number of markets. “It is a safer way to frame for the on-site crew,” Hebert said. “Crews get assistance from cranes to do the heavy lifting and placement of the panels, allowing them to focus on installation. No on-site cutting.”
On the business side, this increased efficiency, consistency, and safety translates into a stronger bottom line for builders and developers. Factory-controlled processes bring ease to the jobsite, making harsh Canada winters much less of a restraint. Plus, fewer callbacks and less waste on the jobsite are big wins for builders, developers, and the environment.
While their proven track record solidifies their position as pioneers in the light-frame wood construction world, a new panel facility in Mount Uniacke, Nova Scotia will be another pivotal move for the company. Slated to open this year, their state-of-the-art 90,000 square-foot facility will manufacture prefabricated walls, roofs, and floors. This move will service the dynamic needs of the light-frame wood construction markets and continue to bring the reliability and quality customers have counted on over the last 35 years.