Weathervane Community Project Big Visions Require Big Teamwork
May 10, 2024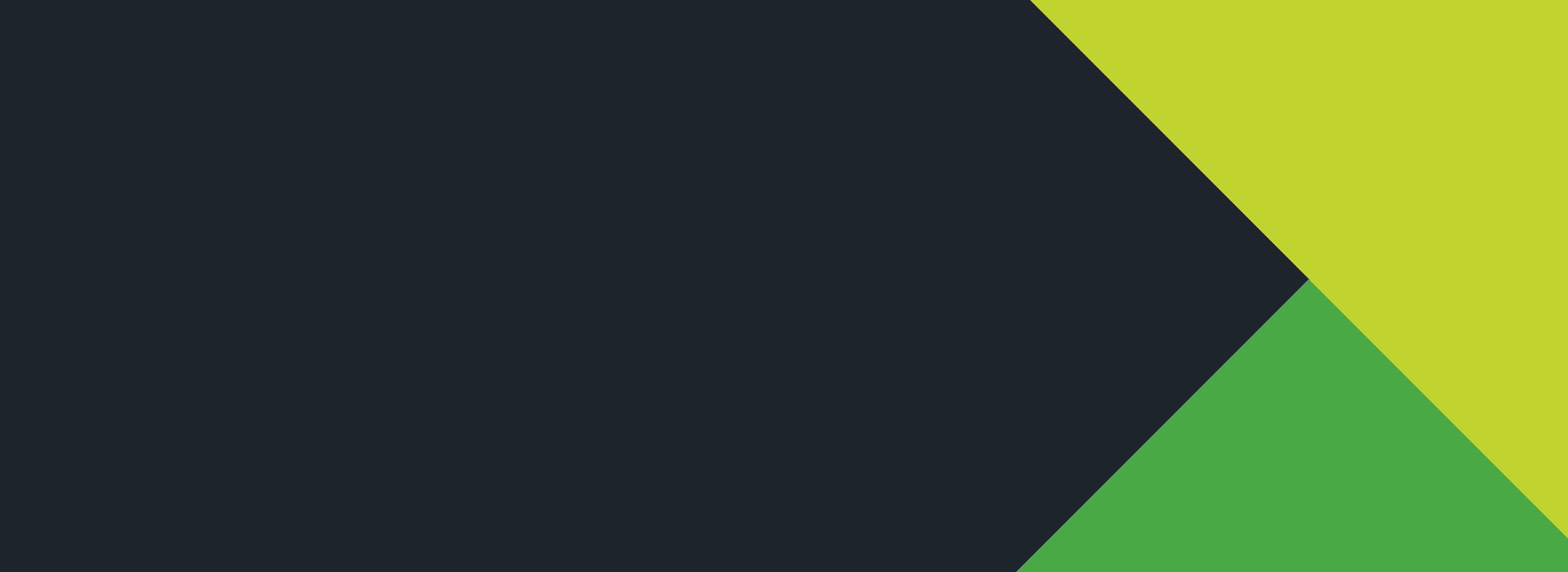
By any measure, Weathervane developer Zocalo Community Development had a big vision: to create a 317-unit LEED-certified multi-family community with 12,000 sq. ft. of commercial space and a myriad of recreational amenities — all built with a deep commitment to sustainability.
For Darrell Chrapko, Boise Cascade Engineered Wood Products’ Multi-Family/Light Commercial Manager, this vision was energizing.
“It was a unicorn project,” he says. “Zocalo has a great reputation, the plans called for 28 miles of EWP, and the finished project was clearly going to be spectacular for the community. We really wanted to be involved.”
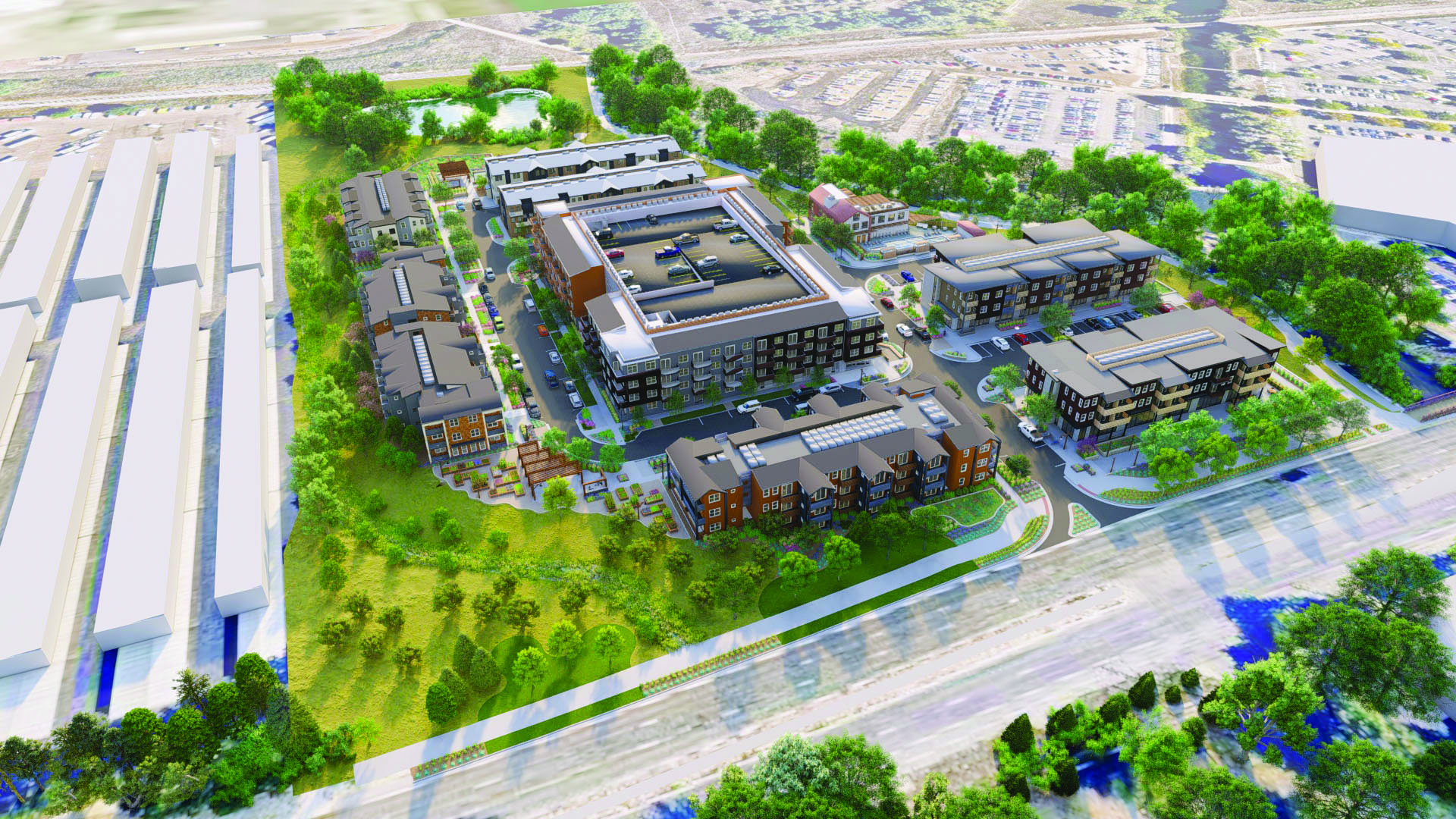
But back in 2021, when the project first came across Chrapko’s desk, just wanting to work on the project wasn’t enough. The entire lumber industry was still responding to the impacts of the pandemic. Supply of many products was limited and on allocation, meaning many builders and developers were limited in what they could get their hands on.
Adding to that the aggressive timelines for the project and ongoing labor shortages, by January 2022 when the project needed to be quoted — effectively locking in Boise Cascade®’s participation, if accepted — the best path forward wasn’t obvious.
“You have to remember the state of the industry at the time, it was in full allocation,” explains Chrapko. “The size of the project was difficult to commit to in 2022, but we knew Boise Cascade and our partners were the right team for the job.”
Getting Together & Getting to Work
Seeing the opportunity, the Boise Cascade team (including both the company’s distribution and manufacturing divisions) worked closely with Matheus Lumber, a national wholesale lumber distributor, to run the numbers and create a plan.
“We were determined to flip over every rock to make this work,” Jeff Sexton, Boise Cascade Building Materials Distribution (BMD) Multi-Family Area Manager, says.
The team sharpened their pencils. They created a proposal that worked hard from every angle, considering material availability, logistics, and customer service needs. The deeper they went, the more the team was convinced Boise Cascade was a natural fit for this project.
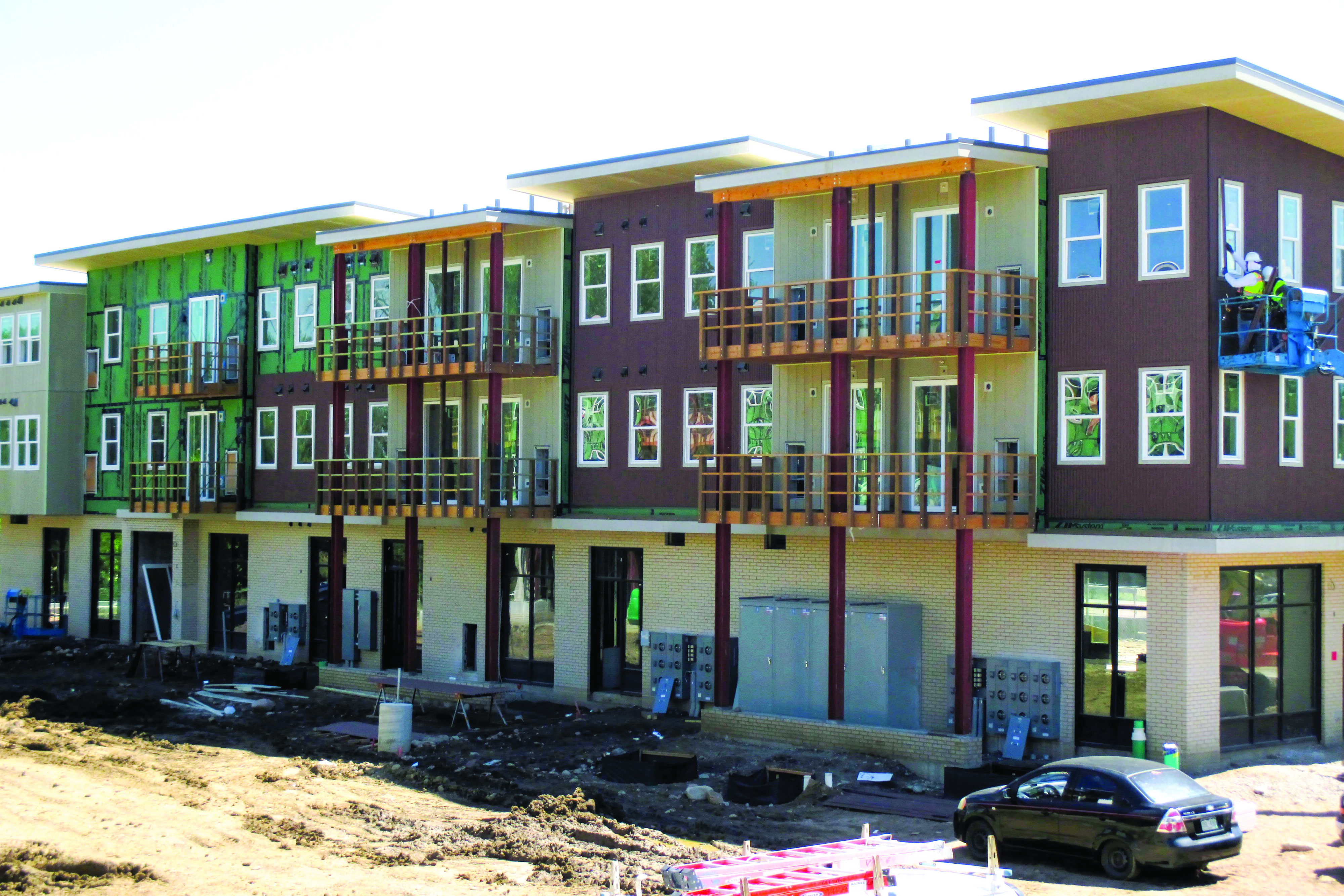
First, the company had the manufacturing capacity to supply it. Yes, it would require them to source product from multiple mills, something that’s not typically done for a single project. But the excellent communication between distribution via Boise Cascade Building Materials Distribution (BMD), manufacturing via Boise Cascade Engineered Wood Products (EWP), and Matheus Lumber made it viable.
The company planned out how they could use capacity and material from both its Alexandria, Louisiana and White City, Oregon mills to deliver product starting in July of 2022 and extending to August of 2023.
Next, they were confident they had the right engineered wood products for the job. Alternative products, namely open web trusses, would push the total height over requirements, forcing the developer to reduce the design by a floor. But the team knew BCI® Joists were strong enough to keep the central mixed-use building at the desired four stories.
“The team at the Denver Boise Cascade is always a pleasure to work with, but on a difficult project they seem to step up even more with expertise on the products and especially engineered wood products on the Weathervane project,” said Brady Tommerup, Idaho Branch Manager with Matheus Lumber Company. “The support and attention to the finer details that Jeff Sexton and Steve Norton provide are unrivaled in that market. Every time we were ready for the next floor, next building, etc., Steve and Jeff were always one step ahead of us with product on the ground ready to cut and ship. Couldn’t have done it without them!”
Finally, they knew they had the experience to get the job done right. Nearly a decade ago, Boise Cascade refocused itself to serve multi-family builders and developers. They began engaging more intentionally with the industry at every level, working closely with APA – The Engineered Wood Association, WoodWorks – Wood Products Council, and others.
In addition, the project team included six people from Boise Cascade’s Building Materials Distribution (BMD) and Wood Products (WP) divisions who were deeply involved: Josh Pounds, WP National Multi-Family/Light Commercial Manager; Brian Harrington, BMD Director of EWP; Jeff Sexton, BMD Multi-Family Area Manager; Darrell Chrapko, WP Western EWP Manager; Cole Gibbs, WP EWP Manager; Jeff Walsh, BMD Senior EWP Designer; and Steve Norton, BMD EWP product manager. All have more than 20 years in the EWP industry.
“It really shows the power of our integrated model,” Harrington explains. “The alignment of our two divisions sets us apart and was the controlling factor in being able to supply a project of the magnitude of Weathervane in an allocated market. Not only highlighting the success of the project but more importantly as a model, in support of Boise Cascade’s ongoing growth in the multifamily segment.”
Once the Boise Cascade team was selected, deliveries, which would total more than 900 tons — 39 truckloads — of materials, began the next month. Products included BCI® Joists, Versa-Lam® LVL, BOISE GLULAM®, and a host of other materials that would be used to build the LEED-Certified project.
Sustainable from the Inside Out
Sustainability is core to the Weathervane design and Zocalo’s corporate values. The company says, on average, Zocalo-designed buildings use 30 to 40 percent less energy than a typical code-compliant building.
Engineered wood, generally, and Boise Cascade’s dedication to environmental stewardship, specifically, fit this approach perfectly.
“Value engineering, carbon sequestration, efficiency of the construction process… Sustainability is a top priority to both Boise Cascade and the industry,” Pounds says.
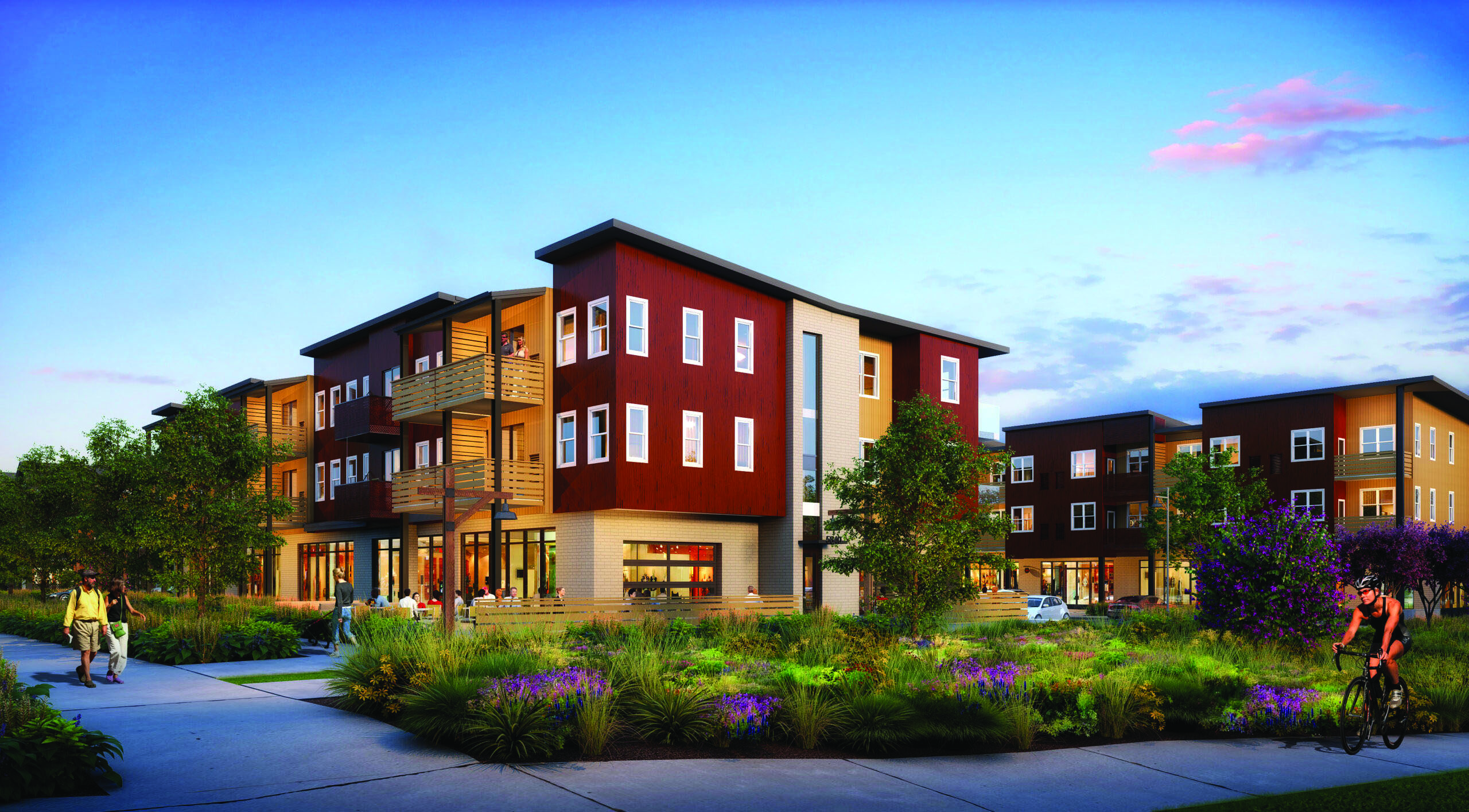
For the Weathervane project, Boise Cascade engaged WoodWorks to generate a carbon summary that detailed the many ways that Boise Cascade EWP reduced or stored carbon emissions over the entire lifecycle of the building.
“Wood remains the ultimate earth-friendly building material,” Pounds says. “As large of a project as Weathervane is at over 272,000 sq. ft., it only takes 13 minutes to grow all the wood or EWP & Lumber that was used.”
Weathervane is a LEED Gold project, the second highest certification level offered by the U.S. Green Building Council. In a sustainability-oriented state like Colorado, this certification not only aligns with the developer’s focus, it is also very attractive to the people and businesses who call Weathervane home.
Teamwork Made the Dream Work
The story of a project as significant as Weathervane could and will be told from many perspectives. But one thing is clear: the way it came together in terms of the structural wood components is a story of teamwork.
From the moment of their introduction to the project by Matheus Lumber, the Boise Cascade team worked across divisions, functions, and time zones to ensure that Zocalo Community Development had the structural solutions it needed.
“From day one, the Boise Cascade and Matheus Lumber teams provided relentless service to Zocalo over the last two years,” said Cory Wight, Zocalo’s Sr. Project Manager. “They exhibited a high level of pride, dedication, and professionalism carried by everyone involved. Their support and assistance helped ensure the project was a success.”
This required coordination and commitment, from the architects and designers to the mills and the logistics crews. Design, production, staging, and even customer support had to communicate readily and regularly.
And they did.
The result is a project that will add to the rich fabric of Boulder for generations to come.
“Our value on this project really shined,” Pounds says. “Zocalo is going to own it and live with it for decades, so our commitment to getting it right not just upfront, but also during construction with technical support, and even over the long-term with customer support, matters in a big way.”