Fading West—A Growing Force in Workforce Housing
September 12, 2024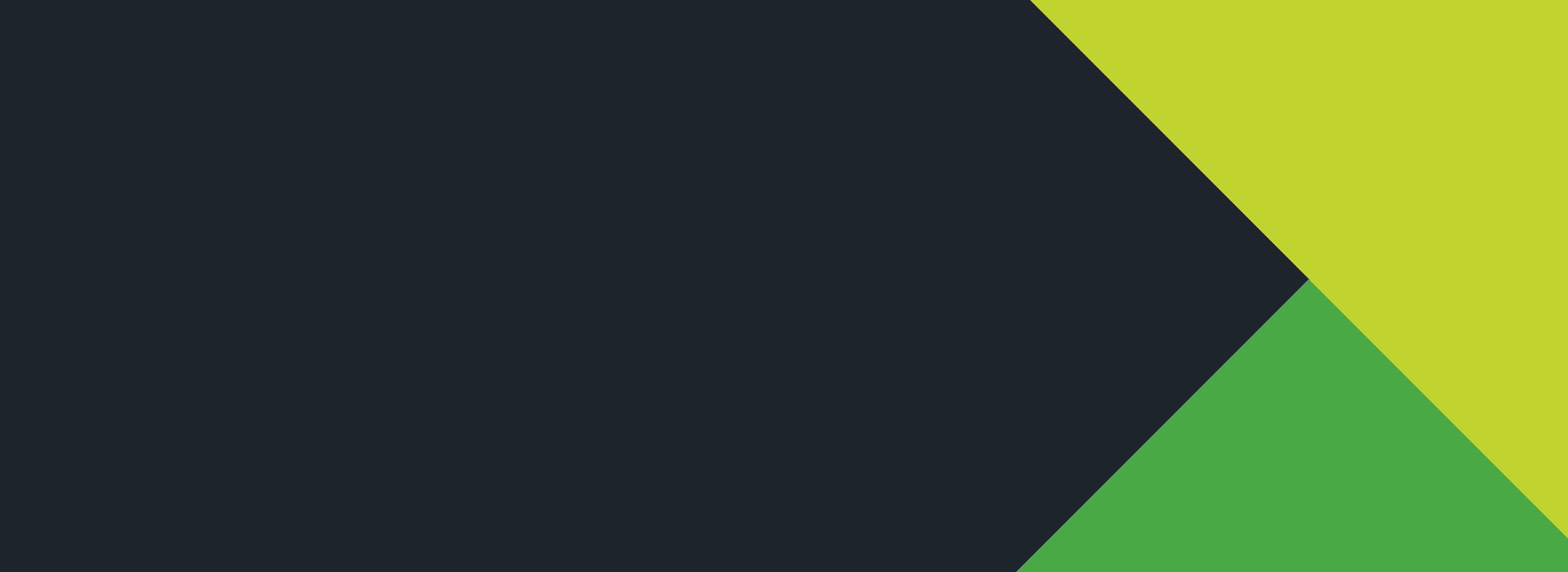
Fading West is bringing high quality modular housing to hard-to-reach (and hard-to-staff) mountain towns… and beyond.
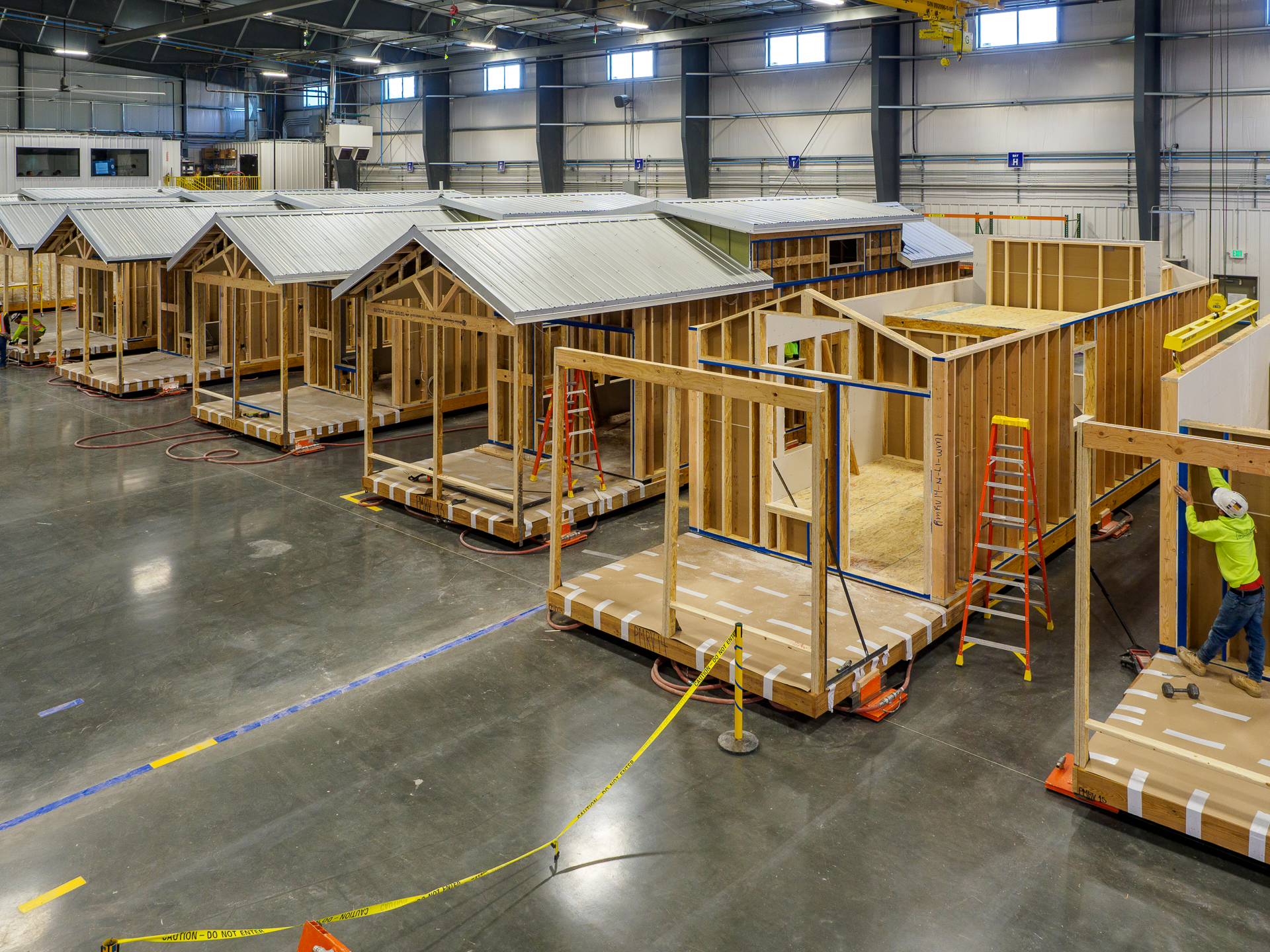
After a couple of decades working in manufacturing, Fading West founder and CEO Charlie Chupp set out to answer a question that had been nagging him for years: how do we create affordable housing in the Rocky Mountains?
Beginning with a single project, The Farm at Buena Vista, Charlie and his team explored the feasibility of creating a small mountain town’s first high density, off-site constructed community.
It worked.
Interest in the homes was high, and the company hit their metrics both in terms of sales and cost structure, despite initially shipping their homes all the way from Nebraska.
The company built on this early success by adding a construction division, doing additional development, and ultimately, creating their own manufacturing facility in Buena Vista, Colorado.
“What sets us apart from other modular housing companies is we started with the doing instead of the selling,” explains Jeremiah Osborn, Fading West’s Supply Chain Director. “We needed workforce housing and the company expanded as the need arose.”
And not surprisingly, yes, the need arose.
Today, the company is busy with projects in other Colorado mountain towns, the Front Range, and several locations further afield. While the building industry continues to struggle to find and train qualified employees, Fading West’s staff of roughly 130 people will produce hundreds of multi-family, microhomes, and single family homes each year in their state-of-the-art 110,000 sq. ft. facility.
While there is cost savings associated with their off-site approach to building, the biggest value driver is predictability, quality, and speed. Off-site construction means fewer weather delays or staffing variability challenges, and more consistency and efficiency in the building process.
“The timeline of construction is condensed,” Osborn says. “We can tell you pretty much exactly when it is going to be ready to occupy.”
For developers of spec homes or rental units, this is particularly important because it gives much clearer visibility into when cash flow will begin. And for companies or cities looking to add workforce housing, this approach means more predictability and less wait time than other options.
The Need for Speed
At Fading West, the homes are built in shippable modules with all interior finishes completed in the factory. This means not only can their manufacturing facility produce one home a day, once the site work is completed, a home can be set on site in less than a day. Their standard designs can be completed — start to finish in the factory— in as little as nine days. When the Fading West team handles the site work, they’ve gone from start to certificate of occupancy in as little as 40 days.
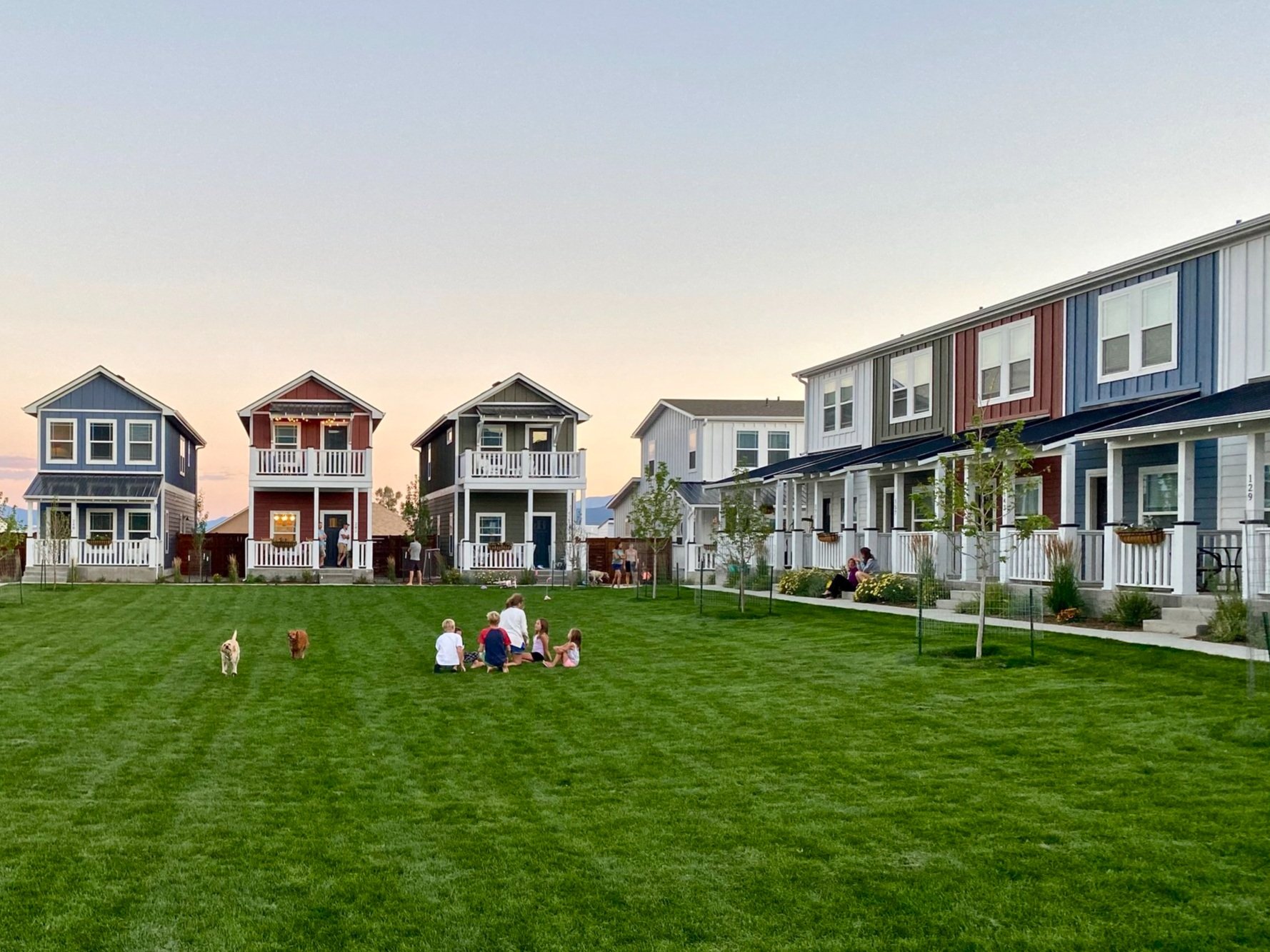
“Speed is really our biggest advantage,” Osborn says.
That speed — while maintaining quality — translates into being able to complete an entire project in a single building season. In more remote or weather-influenced locations, that is a difference maker.
While Fading West builds in a single factory, its homes are shipped to what are often small towns throughout Colorado and beyond. This requires the company to stay up to date with a wide range of code requirements, depending on both the state and the local jurisdiction a project is in.
“Like any builder, we have to keep up with the different codes,” Osborn says. “Each jurisdiction adopts them at a different rate.”
With all that variability at the local level, the company does everything it can to bring efficiency and predictability to the factory building process. Boise Cascade® and, specifically, Boise Cascade Versa-Lam® LVL, play a role in that.
Versa-Lam LVL is recognized as a leader in bending strength and E-value, offering better performance and longer spans. Its consistency, dimensional stability, and lack of camber make it a good fit for Fading West.
While the company utilizes an uncommon size of Versa-Lam LVL to fit their designs and systems, Osborn notes they’ve not had issues with getting the right product when they need it.
“There have been no hiccups,” Osborn says, giving credit to both Boise Cascade and their local distributors, Foxworth-Galbraith Lumber Company. “Both have always been responsive and given us what we needed pretty quickly.”
The key, he says, is understanding the nuances of their business.
“A lot of traditional building materials companies don’t really understand what we do,” he says. “We’re not a builder. We’re not a contractor. We’re a manufacturing company. Boise Cascade has been very good about understanding our business.”
Modular building continues to be a rapidly evolving industry. While this style of construction solves, in whole or part, many of the challenges of the industry — such as local labor, speed of construction, and quality consistency — questions still linger, according to Osborn.
“The biggest challenge is educating the industry on the benefits of modular construction,” he says. “If you have a developer who understands modular well and will standardize their development to better suit modular, you’re going to see a cost savings. But when you want little differences to each house, then modular is not going to be the best option.”
The company’s “sweet spot” projects, according to Osborn, are between 20 and 40 homes, particularly when, “There aren’t many big front range builders who are going to drive up to the mountains to build 20 homes. They’d rather build 300 on the Front Range.”
Workforce Focused
While Fading West takes on a wide range of projects for a wide range of customers, the company is definitely becoming notable as a force in workforce housing.
The company is currently producing a hospital workforce housing project with Aspen Health and a private-public partnership project with the city of Gunnison, Colorado (population 6,800). They recently completed 12 homes for school district employees in the Vail School District in partnership with Habitat for Humanity Vail Valley. Being based in a small city of only 3,000 permanent residents, Fading West even provides housing to its own employees (a benefit that has actually led to a waiting list of potential employees).
The future looks bright for Fading West. The company remains as committed as ever to its founder’s goal of building attainable housing for the workforce — and they continue investing in the necessary innovation to get there.
Learn more about Fading West, the products and projects at www.fadingwestdevelopment.com.